News
Machine Guidance and Autonomous Equipment Meet Contractors Halfway
Aug 9, 2023 - Engineering News-Record
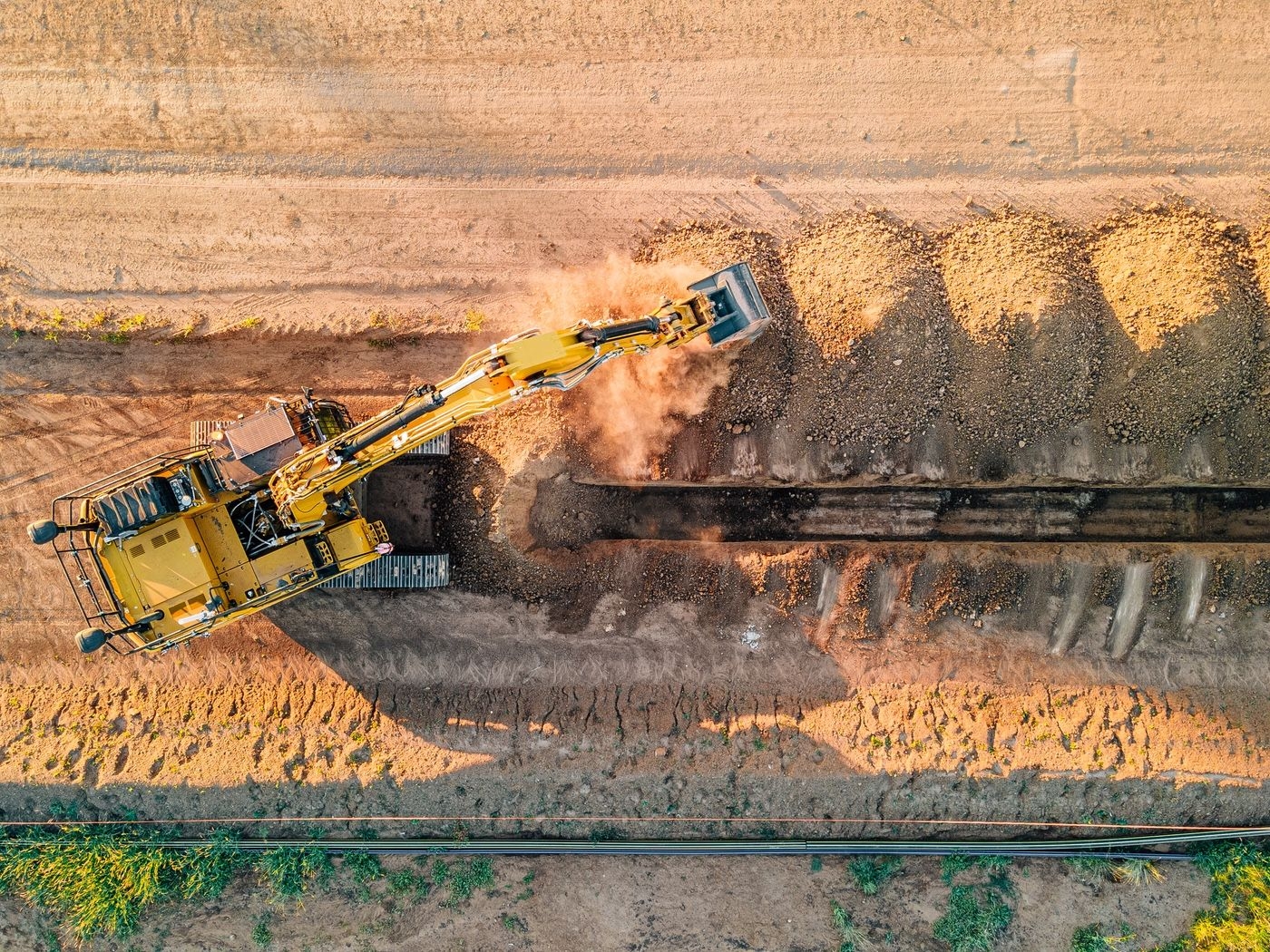
As equipment manufacturers further embrace electrification and autonomous operation, positioning, middleware and robotics technology providers such as Moog Construction, Built Robotics and Trimble are looking to help contractors test the waters of the future.
Switching to electric or autonomous operations is no small expense for contractors. Costs vary, but a battery-powered piece of heavy equipment can have a premium of 50% or more over diesel machines, and that’s before factoring in prices to install charging stations and update service bays.
Aftermarket electrification of diesel-powered equipment can get contractors acclimated to these new systems for a lower price, while dealer-installed sensor packages offer a taste of semi-autonomous machines. Rental channels are another way to try out these new ways of working.
SunBelt Rental took the first 100 units of the all-electric Bobcat T7X compact track loader in 2022, and extended that deal with additional units purchased earlier this year. The T7X has Moog’s integrated software framework, an electric machine controller, lift and tilt electric actuators, electric traction motors, and the formerly diesel engine compartment is filled with batteries and electronic controllers. Its lift runs on electric-powered actuators, not hydraulics, so while it has the power of a regular Bobcat T76 track loader, the battery and controller components makes the T7X about 1,000 lbs heavier, resulting in some different handling for the operator.
Solar Demand Drives Labor-Saving Initiatives
Bechtel Chief Innovation Officer Keith Churchill and Ken Burke, the firm’s global operations manager, worked at the company’s Houston-area equipment yard in 2021 using hardware from Built that allowed the firm’s excavators to be run fully autonomously.
Churchill said a competitive labor market made it advantageous for the major EPC contractor’s skilled operators to oversee several of the autonomous excavators from a trailer rather than spend hours at a time digging trenches for large solar farm projects in Texas and Louisiana.
Operators could monitor the Komatsu and Caterpillar excavators on site as they dug ditches for electrical lines and holes for piles to support the panels. Built’s system was tested by Burke and his team at Bechtel’s yard, and they came up with improvements such as using a safety geofence to make sure the excavators automatically shut down if they got too close to humans. Built’s system fits onto regular Caterpillar and Komatsu hydraulic excavators, turning the machine’s electrohydraulic controls over to an onboard computer programmed to perform standardized and repetitive excavation tasks as loaded prior to operation. On Bechtel’s solar projects, Built-enabled excavators achieved a 93% uptime at a productivity rate of 191 linear ft per hour—a 45% productivity increase over a single operator digging trenches.
READ THE FULL STORY